How To Choose The Correct Warehouse Management System
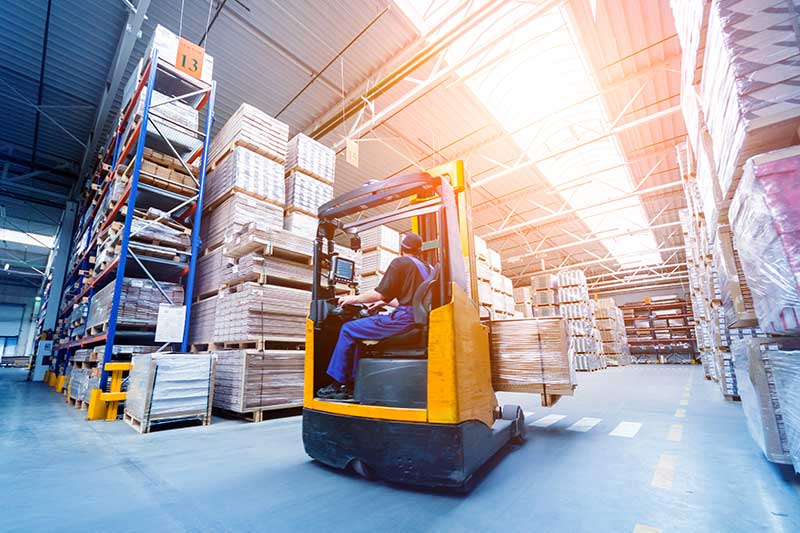
Because 3PL (the abbreviation of third-party logistics) warehousing is constantly evolving, one’s operation may experience several changes over the years. That’s why growing 3PLs are recommended to employ a warehouse management system (WMS) that adapts and changes with their businesses. Because there is a wide range of warehouses operating in the logistics vertical today, there is an abundance of software to choose from. Before starting your search for the perfect WMS, it is important to first identify several key traits about your warehouse.
Understand Your Shipments
Does your business specialize in assembling and kitting; carton in/carton out; or pallet in/pallet out (cross-docking)? It is recommended that business owners choose a WMS technology that can automate existing workflows and enable hands-free shipping, packing, and picking. With the rise of e-commerce, achieving 100 percent order accuracy will be invaluable to your customers as you scale together.
Identify Products that Require Storage
Another step you can take is to identify all the types of products that are currently stored in the warehouse, as well as items that may be stored in the future. By gaining a clear picture on which type of warehouse you want to operate, the more specific you can be in the software selection process. For example, if you store products with expiry dates (e.g., beauty and makeup products), consider installing a WMS that facilitates a First-In, First-Out (FIFO) distribution model. Alternatively, one may utilize a WMS that tracks catch weights if the business focuses on grocery distribution.
Notice How Customers Place Orders
Today, having a WMS that accommodates how one’s customers place their orders is more important than ever. Below is a quick look at some of the most common order placement methods:
- Retail/Electronic Data Interchange (EDI): Large retail customers often prefer to establish EDI connections when ordering. Choose a reliable WMS that can manage and facilitate these connections.
- API/Shopping Carts: If your warehouse serves omnichannel or e-commerce customers, the chosen WMS should come with the ability to add shopping cart integrations, e.g., with ShipStation, Amazon, WooCommerce, and Shopify.
- Spreadsheets: Some customers may place their orders by sending CSV or other Excel files. Your selected WMS should have an easy to use import function.
- Manual: While allowing customers to place orders via phone call or email may seem harmless at first, receiving this information requires manual work. In addition, it may increase the risk of human error that affect one’s bottom-line. A smarter solution is to offer customers a dedicated portal where they can place orders directly into your system and/or check the latest inventory status.
Consider the Number of Customers You Serve
It is now common for warehouses to serve multiple customers that sell through different channels. Business owners need to start considering how to better receive each customer’s orders, store and manage their inventories, and manage billing matters so that each customer’s data is kept separate. With that said, you may want a WMS that brings together multiple technologies: billing, mobile device shipping and picking workflows, automated receiving processes, and shopping carts.